Supplier announcements about new nucleating and clarifying agents have become among the most frequent ones related to any additives used for polyolefins. Directing their attention mainly at polypropylene (PP), makers of clarifying agents in particular have been trying to expand PP into packaging applications that allow clarified PP (CPP) to compete directly with PET. Clarifiers may also allow cPP to enter clear container sectors that PET cannot enter, such as hot-filled food and beverage containers. Yet nucleating agents, of which clarifying agents are a subcategory, offer multiple property improvements in polyolefins by promoting the fast, controlled formation of fine spherulite crystal regions throughout the volume of the resin product. This chapter will tend to focus on PP, since its crystallization rate is slow enough to allow nucleating agents to significantly affect its crystallization properties. However, the idea of using nucleating agents for improving fast-crystallizing polyethylene has drawn increasing attention as well.
Nucleating Agents
Designed nucleating agents for controlled nucleation allow crystallization temperatures to be increased by as much as 20°C or more for PP (and 2-5°C for polyethylene, whose crystallization can only be minimally enhanced by a nucleator). By effectively raising the crystallization temperature and increasing the possible sites and rates of crystallization, nucleating agents are used for creating more dimensionally stable parts, higher mechanical properties, quicker processing (solidification) times, and often higher clarity. The ultimate number and size of the spherulites and total fraction of crystallization in the matrix ultimately determines how much the resin’s properties and processing are affected by the agent.
Nucleating agents may simply be used to enhance physical properties and processing, but the industry has also created clarifying agents as a class of nucleating agents that specifically effect optical properties. These agents create spherulites that are smaller than the wavelengths of visible light (400-700 nm); thus, light is not scattered by the crystal regions, and there is little opacity in the resin product. Experts have also categorized nucleators as being melt insensitive (where the agent does not melt with the resin) and melt sensitive (when the agent’s melting point is near that of the resin). Melt-insensitive agents are metal organic salts, and some are clarifiers; meltsensitive agents tend to be fully organic and are usually clarifiers. Some of these distinctions are summarized in blew table:
Primary Purpose | Additives | Commerical Products | Common Materials/ Application | Application |
Nucleation | Carboxylic acid salts | Sodium benzoate, Milliken
HPN-68 |
PP | Traditional and fast (“hyper”) nucleators enhance physical properties and productivity and reduce warpage |
Fine talc or other fine mineral fillers | Rio Tinto Luzenac and Jetfine | PP | Increased stiffness and crystallization temperature (short cycle times) | |
Nucleation and clarification | Organophosphate salts/esters | ADK Stab
NA-11 NA-21 |
PP | Fast, efficient nucleation/ clarification |
Trisamide | BASF
Irgaclear XT 386 |
PP | Low haze at 1/10th the concentration of sorbitol clarifiers; cycle-time reduction | |
Carboxylic acid salt | Milliken
HPN-20E; Ingenia IP1810 |
LDPE film | Haze reduction and higher gloss and physical properties | |
Clarification | DBS and MDBS (trad. sorbitols) | Multiple | PP | DBS: plate out limitations;
MDBS: organoleptic (taste/ odor) limitations |
DMDBS (“third-gen.” sorbitol) | Milliken
Millad 3988 |
PP | Overcomes most previous sorbitol limitations | |
Nonitol | Milliken
NX8000 |
PP | Higher level of “water white” clarity possible; replacing DMDBS/Milled
3988 |
Nucleating Agent Effects on Processing and Properties
As particles distributed within a matrix, nonmelting nucleating agents create multiple single point nucleation sites for crystallized regions to grow around. Mechanisms of nucleating and clarifying agents show blew figure.

(A) The increasing crystallization (gray regions) around nucleating agent particles in the polymer over time, left to right. (B) How a fibrous, melt-sensitive clarifying agent creates a network of nucleation sites, creating very small crystalline regions that are too small to scatter light.
Traditional agents include aromatic carboxylic acid salts such as sodium benzoate, which is mainly used for enhancing physical properties, and metal salts of phosphate esters, which both clarify the resin and enhance properties. The amount of clarity gained is dependent on the number of nucleation sites created, the size of the nucleator particles, and the amount of dispersion that occurs when the agent is mixed with the polymer. Finer particle sizes generally make for more effective nucleators, and even the particle shape has been said to determine nucleation effectiveness. Oriented, “needle-like” crystal shapes produced by traditional agents are considered inferior to “plate-like” shapes for encouraging isotropic shrinkage. Thus, phosphate ester salts, for example, with their needle-like shapes, promote radial, in-plane crystal growth mainly in the polymer flow direction during molding, potentially creating uneven shrinkage and thus warpage later. By contrast, a carboxylic acid salt agent like Milliken’s HPN-20E, with particles described as “ruler shaped,” is said to promote in-plane crystal growth in both the machine-flow and transverse-flow directions, leading to low, isotropic shrinkage. Likewise, thermal expansion and stiffness can be shown to be improved by the agent in both directions, rather than just the flow direction. Nucleating agents provide processing advantages. In injection molding, they allow parts to be removed from the mold at higher temperatures, resulting in shorter cycle times.
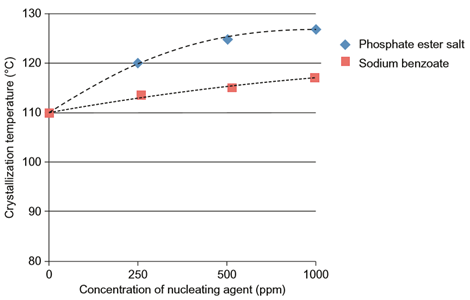
Advantages:
Reduces haze in injection molded items
• Increases the transparency
• Improves the dimensional stability
• Increase the stiffness and heat deflection temperature
Lowers the cycle time for moulding process
Applications :
• Injection molded items
If you intend to buy nucleating and clarifiers PP, You can call 02158381200 for consultation, order and buy this masterbatch.