An additive is a substance that is incorporated into plastics to achieve a technical effect in the finished product and is intended to be an essential part of the finished article. Some examples of additives are antioxidants, antistatic agents, antifogging agents, emulsifiers, fillers, impact modifiers, lubricants, plasticizers, release agents, solvents, stabilizers, thickeners and UV absorbers. Additives may be either organic (e.g., alkyl phenols, hydroxy benzophenones), inorganic (e.g., oxides, salts, fillers) or organometallic (e.g., metal carboxylates, Ni complexes, Zn accelerators).
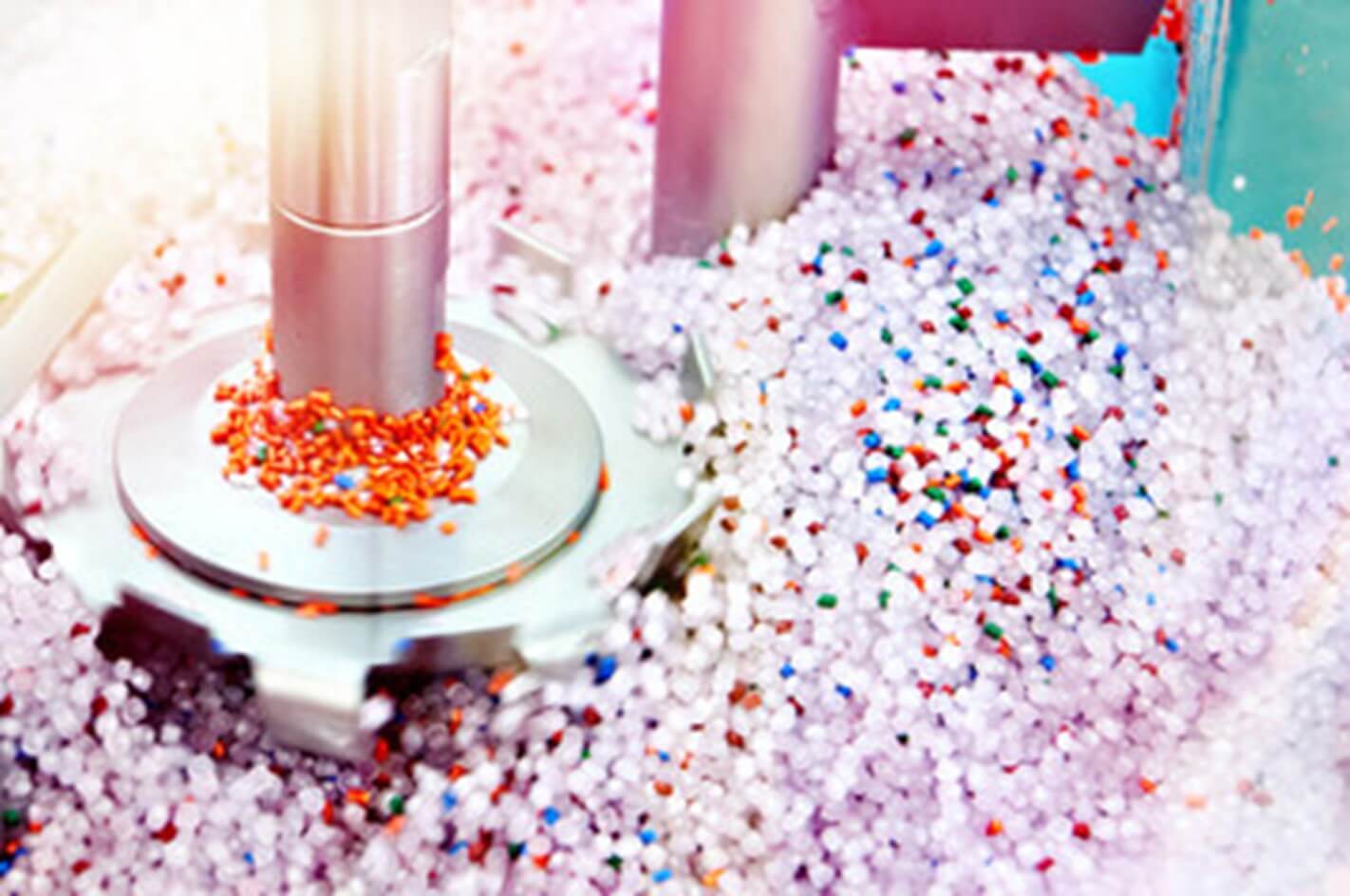
Since the very early stages of the development of the polymer industry, it was realized that useful materials could only be obtained if certain additives were incorporated into the polymer matrix, in a process normally known as ‘compounding’. Additives confer on plastics significant extensions of properties in one or more directions, such as general durability, stiffness and strength, impact resistance, thermal resistance, resistance to flexure and wear, acoustic isolation, etc. The steady increase in demand for plastic products by industry and consumers shows that plastic materials are becoming more performing and are capturing the classical fields of other materials. This evolution is also reflected in higher service temperature, dynamic and mechanical strength, stronger resistance against chemicals or radiation, and odorless formulations. Consequently, a modern plastic part often represents a high-technology product of material science with the material’s properties being not in the least part attributable to additives. Additives (and fillers), in the broadest sense, are essential ingredients of a manufactured polymeric material. An additive can be a primary ingredient that forms an integral part of the end product’s basic characteristics, or a secondary ingredient that functions to improve performance and/or durability. Polypropylene is an outstanding example showing how polymer additives can change a vulnerable and unstable macromolecular material into a high-volume market product. The expansion of polyolefin applications into various areas of industrial and everyday use was in most cases achieved due to the employment of such specialty chemicals.
Plastic additives are a diverse group of specialty chemicals that are either incorporated into the plastic product prior to or during processing or applied to the surface of the product when processing has been completed. To a great extent, the selection of the appropriate additive is the responsibility of the plastic processor or the compounder carrying out the modification. The blow Scheme illustrates the use of typical additives in the process from polymerization to product manufacturing.
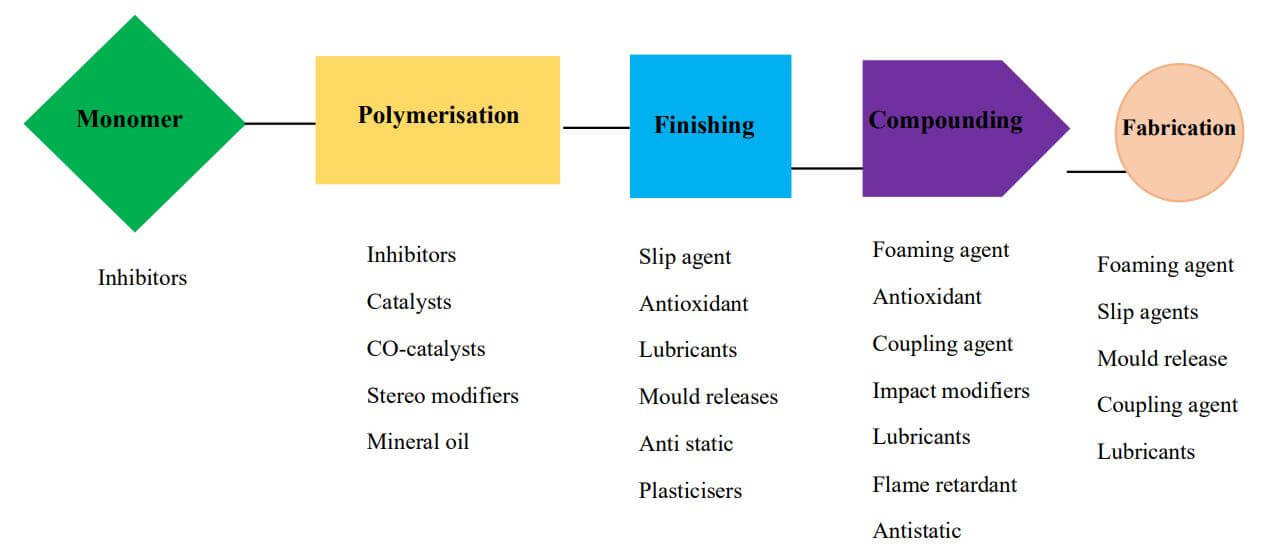
For instance, Basic additives used for polypropylene include:
- Long-term stabilizer (always for Z/N PP, usually phenolic AOs)
- Melt stabiliser (phosphite or phosphonite)
- Acid scavenger (always for Z/N PP)
- Slip and antiblocking agents (for film)
- Nucleators, clarifiers, antistatics (for specific injectiomolding)
- Specific antioxidants (for fibres, nonvolatiles, gas-fading
- UV absorbers (for automotive)
Main types of additives for plastics and their functions:
Functions |
Examples |
Type |
Adding bulk to a compound: increasingly used to improve stiffness, surface hardness |
Calcium carbonate, talc, mica |
Filler s and mineral reinforcements |
Mechanical strength: used as short fibre, long fiber, spheres |
Aramid, carbon, glass, natural fibers |
Fibre reinforcements |
Virtually unlimited, added as powders or liquids: easier mixing, replacement of heavy metals |
Pigments, liquid colors, color pastes, dyestuffs, special effects |
Colorants |
Also for improved UV resistance and (carbon black) electrical conductivity |
Carbon black, titanium dioxide |
Black and white pigments |
Act to delay/prevent oxidation of polymer under heat, during processing or application |
Antioxidants and stabilizers |
Heat resistance |
Delay/prevent oxidation of end-product under prolonged exposure to sunlight |
UV stabilizers |
UV resistance |
Prevent ignition of polymer, promote extinguishing: types not producing smoke or fumes |
Reactive, additive, and other systems |
Flame retardants |
Increase electrical conductivity, to prevent electrostatic discharge, sticking/clinging (e.g. films) |
Antistatic/conductive additives |
Antistatics, conductives |
Initiate and control the cure of thermosetting resins |
Accelerators, curing agents, and catalysts |
Curing systems for thermosets |
Cross-linking agents for thermoplastics; coupling agents, compatibilizers to promote bonds between polymers and additives |
Forming cross-links between suitable polymers and other molecules |
Cross-linking, coupling, compatibilizing |
Improvement in processability, and flexibility: used mainly in PVC, but limited use in other plastics |
Mainly phthalates, but many systems are used |
Plasticizers |
Improvement of mixing/blending; control of viscosity |
Lubricants and plasticizers, nucleating agents |
Process modifiers, processing aids |
Production of foams and expanded plastics; replacement of chlorofluorocarbons (CFCs) |
Inert gas or gas-forming chemicals injected or mixed into a compound to react during processing |
Blowing agents |
Improvement in processing; release properties; reduced slippage and blocking with films |
Lubricants, mold release agents, slip and anti-block |
Lubricants |
Giving specific properties |
Barrier properties, shrinkage, acoustics, surfactants, antimicrobials |
Other types |
Used to improve/protect properties of waste plastics during mechanical recycling |
Impact modifiers, stabilizers |
RecycUng additives |
You can order, receive or price additional masterbatches by contacting 02158381200 if you would like to order and buy additional masterbatch.